Project Spotlight: Lynchburg Regional Airport (LYH) Uses StellarFlex FR® for Apron Rehabilitation
/in Product Innovation, Projects/by Emily Ann WatersProject Spotlight: Unique Funding Program Supports Repaving with FlexGard® in York County
/in Product Innovation, Projects/by Emily Ann WatersIn October of 2020, Associated Asphalt partnered with Blythe Construction and York County, South Carolina to repave 1.5 miles of roadway on Penshurst Road in Rock Hill. Associated Asphalt’s Greensboro Terminal provided 121 tons of FlexGard® binder for the overlay to boost pavement life and cracking resistance.
The Cost-Savings Advantage of FlexGard®
The original scope for the Penshurst Road project required a cement-modified recycled base at a uniform depth of 10 inches, followed by a 2-inch layer of SCDOT hot mix surface type. Sr. Technical Services & Marketing Manager, Robbie Robinson, was in charge of inspecting the site to provide recommendations.
Upon further evaluation, Robinson recommended the use of FlexGard® in lieu of the original scope, which included a full-depth reclamation. There were very few areas that showed base failure, despite the severe end-of-life characteristics of severe alligator cracking. This recommendation resulted in a revised scope of work that would include a 1.75-inch overlay of FlexGard®, reducing the cost of the project by $26,000. The unique thinning of asphalt in certain areas of the roadway led the team to agree upon a slightly thicker overlay rather than a traditional thin overlay.
The FlexGard® System features a slightly gap-graded mix gradation combined with a polymer-modified asphalt designed for thin, high-performance overlays.
The FlexGard® mix also incorporates a StellarFlex® polymer modified asphalt. Selected according to roadway conditions and demands, StellarFlex® binder further boosts pavement life and cracking resistance. FlexGard® has a relatively high binder content that allows for easier field compaction and lower air voids in the finished layer.
FlexGard® includes a complete set of specifications that local owner agencies can use to advertise and administer the contract. The FlexGard® mixture must meet a maximum rutting depth and a minimum number of cycles to failure on the Texas Overlay Tester (a cracking test procedure).
About Pennies for Progress
Funding for infrastructure updates has always been a hot topic for government entities, industrial organizations, and the transportation industry. There are many challenges when it comes to managing budgets that can support these high investment projects.
York County, SC has taken a unique approach to provide citizens with a safer and more efficient roadway system. Pennies for Progress is the name of the York County Capital Projects Sales and Use Tax Programs. As the principal source of road improvement funding, York County voters have the opportunity to vote on what projects will be chosen for improvement. It is the first of its kind in South Carolina.
Become a Partner
Are you looking for cost-savings opportunities for your next repaving project? Associated Asphalt experts are available to inspect your roadways and make custom recommendations for your project.
Project Spotlight: Repaving Carolina Motorsports Park
/in Product Innovation, Projects/by Emily Ann Waters2020 has brought new challenges to everyone, but some businesses like Carolina Motorsports Park have been able to maintain steady progress. The Cummings family took over operations of Carolina Motorsports Park in Kershaw, SC in late 2019 under a lease. By mid-June 2020, they became full owners of the property and have been “pedal to the metal” on updating the property ever since!
We spoke with Michael Cummings Jr., who wears many hats at the park, about the history of the park, his family’s involvement in its revitalization, and the major track resurfacing project Associated Asphalt was chosen to supply the asphalt binder during July of 2020.
History of Carolina Motorsports Park
Carolina Motorsports Park originated in 1999, created by a group of enthusiasts and racers who wanted a place to practice. The park was built on an old airport called “Kershaw Airport” and hosted a variety of events, including NASCAR test runs, in its prime. In 2016, the park was put up for sale. While the park remained open during the transfer of ownership, some of the tracks and facilities were not maintained as they should be.
The current owner, Michael Cummings Sr., has a long history in the racing and motorsports industry, previously as a racer, and now on the business administration side. Cummings runs a financial consulting firm, Motorsports Capital, LLC. When he found out Carolina Motorsports Park was for sale, he tried to help the park by finding a purchaser. Finally, he decided it was time to invest in the property himself.
Resurfacing the Track
In late 2018, the Cummings family began planning out what updates they would make to the park and started discussions with racetrack consulting engineers, Advanced Materials Services LLC from Auburn, AL, to engineer a major resurfacing project for the park’s 2.27 mile-long track. This would be the first time the track has been repaved in its entirety.
Fast forward to 2020, Associated Asphalt was called upon by Lynches River Contracting to provide 294 tons of a specially formulated asphalt binder for the top layer of asphalt.
This specially formulated asphalt binder had to meet the softening point criteria, as set forth by the consulting engineer, thus increasing the durability of the new asphalt layer. The project took place over the first few weeks of July and the track celebrated a grand re-opening and ribbon cutting on August 14.
“Everyone was extremely professional,” says Michael Cummings, Jr. “A few of our peers even came to visit during the project and were extremely impressed by the level of detail and engineering involved in the project.”
Watch the project in action on the Carolina Motorsports Facebook Page.
What’s Around the Next Turn?
Since taking ownership of the park, Carolina Motorsports Park has hosted a variety of events on their three tracks: the 2.27 mile road course, a 0.7 mile gocart track, and a 200 foot skid pad. Upon re-opening the road course, they’ve only received praise from the drivers enjoying the freshly paved track.
“We had three groups of motorcyclists on the track just a few weeks after re-opening. They’re always the hardest to please when it comes to having a smooth track and we didn’t get a single complaint,” says Cummings Jr.
Carolina Motorsports Park plans to continue to make improvements to the facilities to provide the best high-speed experience possible to all patrons. They feel confident knowing that their investment in a resurfaced track will pay dividends for years to come. Check out their calendar of events to watch the track in action or take a drive yourself! You may get lucky and catch Jeff Gordon on one of his visits to the track.
Become a Partner
Associated Asphalt can provide a wide variety of standard and specialty asphalt products to fit a variety of paving specifications. To learn more about how our network of terminals can support your next project, contact us today.
Project Spotlight: Chesapeake Bay Bridge-Tunnel
/in Product Innovation, Projects/by Emily Ann WatersPhoto Credit: Allan Myers
In April of 1964, the Chesapeake Bay Bridge-Tunnel (CBBT) officially opened to traffic after a 42-month project fondly referred to as “when men split the sea“. For more than 50 years, the CBBT has captured worldwide attention as an award-winning modern engineering marvel, crossing over and under the open waters of the Chesapeake Bay. With over 130 million commercial and passenger vehicles having crossed the Bridge-Tunnel, the incredible structure had seen it’s fair share of wear and tear.
Milling and Repaving Project
In July 2019, Allan Myers was awarded a milling and repaving project and partnered with Associated Asphalt to supply a highly modified asphalt. The project would require the milling and replacement of asphalt to level the surface from the south toll plaza and the north toll plaza in both northbound and southbound lanes.
For this particular project, we supplied 2,100 liquid tons of Highly Modified Asphalt, PG 76E-28. StellarFlex® HiMA is formulated to provide extreme resistance to permanent deformation, fatigue cracking, and thermal cracking, which prove to be common threats to asphalt durability.
Paving began in September 2019, paused from November 2019 – February 2020, and is expected to be completed in June 2020.
As a company based in Virginia, it was an honor to have the opportunity to supply asphalt to restrengthen and revitalize such an internationally recognized structure. We look forward to watching the rest of the Parallel Thimble Shoals Tunnel Project come to completion.
About StellarFlex® HiMA
Formulated to provide extreme resistance to permanent deformation, fatigue cracking, and thermal cracking, StellarFlex® HiMA is a very highly Styrene-Butadiene-Styrene (SBS) polymer-modified asphalt. Featuring three times the polymer typically found in standard polymer-modified asphalts, StellarFlex® HiMA is an ideal asphalt binder for bridge deck paving applications, or to limit cracking over concrete pavements.
Contact us to see if StellarFlex® is the right product for your project.
Project Spotlight: LaBelle Municipal Airport Uses StellarFlex FR® For Apron Rehab Project
/in Product Innovation, Projects/by Emily Ann WatersProject Highlight: Laying StellarFlex FR® at Hollywood-Burbank Airport
/in Product Innovation, Projects/by Emily Ann WatersProject Highlight: Applying StellarFlex FR® to St. Augustine Horse Paths
/in Impact, Product Innovation, Projects/by Emily Ann WatersIf you’ve ever paid a visit to the historic St. Augustine, FL, it’s likely you’ve seen one of their famous horse-drawn carriage tours pass by. These rides allow visitors and residents to take in the stunning historic architecture and culture of the city from the comfort of an open air carriage. Riders rely on a smooth path to make the experience relaxing and enjoyable. Earlier this year, Associated Asphalt teamed up with Duval Asphalt and Asphalt Testing Solutions & Engineering to assure a smooth ride for passengers by repairing the deteriorated horse paths and providing protection from future rutting.
[image url=”https://associatedasph.wpenginepowered.com/wp-content/uploads/2019/10/St.-Augustine-3.jpg” alt=”” size=”large” caption=””]
St. Augustine Project Background
In 2015, the Florida Department of Transportation (FDOT) funded a maintenance project on State Route 5A to reduce rutting and smooth out the path where the horses and carriages had caused the most deterioration. Following the lead of Central Park’s application of a fuel-resistant binder for their own horse-drawn carriage paths, FDOT awarded Jacksonville’s Duval Asphalt the maintenance project to mill 1.5 inches of friction course and lay the new fuel-resistant mix.
In 2019, after proof that the fuel-resistant mix would hold up against the wear and tear of constant horse-drawn carriage traffic, a full reconstruction was ordered. Once again, the project was awarded to Duval Asphalt. Asphalt Testing Solutions & Engineering (ATS) was brought in to oversee quality control of the product mixing and placement.
[image url=”https://associatedasph.wpenginepowered.com/wp-content/uploads/2019/10/St.-Augustine-2-2.jpg” alt=”” size=”large” caption=””]
Application of StellarFlex FR®
Historically, StellarFlex FR® is applied to airport landing strips and taxiways to provide fuel resistant protection. Because this paving project would need protection from the asphalt softening effect of horse urine, rather than jet fuel spills, specifications needed to be adjusted. Associated Asphalt worked with ATS to adjust the fuel-resistant mix to perform for FDOT and project specifications under the exposure of the animal waste and pressure of the thin carriage wheels. 350 tons of the fuel-resistant mix was applied to the horse paths. The reconstruction project is expected to last another 15 years before further maintenance is needed. With this new extended lifespan, the large investment in quality paving materials will prove to be the most economic solution in the long run.
Related Reading
Due to the unique nature of the project’s challenges and solutions, the St. Augustine collaboration has been spotlighted in multiple industry publications. To learn more about the project and hear from team members who worked directly on the project, check out these articles by AsphaltPro Magazine and Asphalt Pavement Digital.
Do you have a unique paving challenge? Become an Associated Asphalt Partner to help pave the way to success.
Project Highlight: Laying StellarFlex FR® at Georgetown County Airport
/in Product Innovation, Projects/by Emily Ann WatersLaboratory Performance of Fuel Resistant Hot Mix Asphalt
/in Impact, News, Product Innovation/by Emily Ann Waters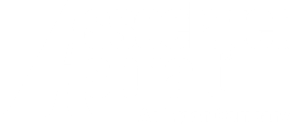
Physical Address
9th Floor
Roanoke, VA 24011
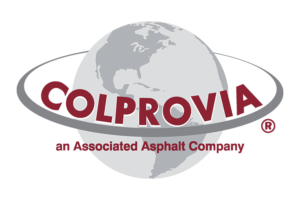
Mailing Address
Roanoke, VA 24027

Phone Numbers
800-542-5780 (Toll-Free)
540-345-2470 (Fax)
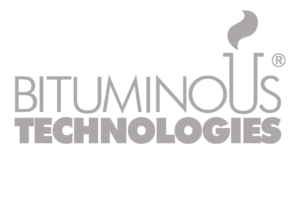